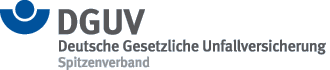
completed 03/2019
3D printers are being used increasingly frequently in companies. The aim of the project was to conduct measurements to determine the inhalative exposure to hazardous substances, including ultrafine particles, during work on additive manufacturing machines in universities and commercial businesses. These include engineering consultancies, dental laboratories, universities of technology, institutes, and enterprises of a similar nature. Particular attention was to be paid to the materials employed, such as various plastics in wire and powder form, metals, metal alloys, and ceramics. Where exposure was found to be significant, the results of the study were to serve as a basis for a sector-specific guidance document describing protective measures by which exposure is to be reduced to a minimum.
In conjunction with the German Social Accident Insurance Institutions for the public sector, data were to be obtained on emissions from the 3D printers in use, for assessment of the existing situation in businesses and universities in Germany. For this purpose, guidance documents were produced governing the measurement procedure, including recording of the data as part of the measurement campaign 9186, Emissions from 3D printers. Measurements conducted in test chambers were also to examine the various printer materials with respect to their emissions.
In the course of the project, the additive procedures were divided into three categories: The metal powder-(bed-)processes; plastic powder processes; and desktop 3D printers with test chamber measurements. In the majority of metal power-(bed-)based methods, the manufacturing process involves similar steps and comparable exposure scenarios. Provided the equipment has not been modified, it is generally so leak-tight that no exposure to hazardous substances need be anticipated during the manufacturing process. On the systems studied, in which metal powder containing chromium was used, no chromium (VI) compounds were detected in the workplace atmosphere. Work involving nickel-based and cobalt-based alloys requires technical measures to be taken, since the assessment criteria could otherwise be exceeded. This particularly applies to work with open powders, or work on the component before it has been depowdered. Besides the metal-processing systems, the systems processing plastic powders account for a large proportion of the applications. Polyamide-based plastics are generally processed in these systems. To date, no measurable inhalative exposure to hazardous substances has been determined in these laser-sintering methods, provided normal laboratory practice is followed. New materials are however continually being developed. These include materials to which fillers are added, which for example may also include fibres. Results The small desktop 3D printers, which generally employ plastic wire as the raw material, have attracted substantially more media interest in recent years. According to present information, the RW I recommended levels or IRW indoor workplace reference levels are observed, provided the room in which the printer is located is ventilated sufficiently and regularly. A particular characteristic of the desktop printers is the variety of plastics that can be used. Owing to the differences between their fusion temperatures, it must be ensured on this equipment in particular that the materials employed are not heated above their decomposition temperature. Studies in the test chamber employing a range of plastics confirmed the results of the measurements made at universities and commercial businesses.
-cross sectoral-
Type of hazard:dangerous substances
Catchwords:exposure
Description, key words:3D printer