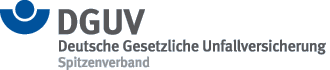
completed 12/2009
In order to limit workplace exposure to emissions from metal working fluids comprehensive measurements are needed. Besides monitoring, maintenance and care of the metal working fluids as well as par-ticular engineered protective measures are required for collection and filtration of the emitted substances and for an effective ventilation. Numerous measurements taken by the institutions for statutory accident insurance and prevention and the Institute for Occupational Safety and Health (BGIA) have shown that with only a few exceptions, the exhausted air is not adequately purified in the wide variety of collection systems, and that excessive mass flows are returned to the working area. Within the project, a test facility was to be developed with the aid of which collection and filtration systems could be optimized and tested.
Based upon the results of the work carried out in the project entitled "Exhaust and filtration of metal working fluids emissions on machine tools" (BGIA 3093), a test facility for metal working fluid filters was erected and retracted. In order to enable all filters to be tested under identical conditions, the test facility was supplied with conditioned air. For validation of the results from the test facility, a simulation analysis was also performed of the fractional filtration, since this may vary in the filter according to the liquid/vapour equilibrium.
A test facility for cooling lubricant filters was developed and erected at the BGIA for the purpose of the project. The test facility contains three main elements: metering system, untreated gas measurement system and purified gas measurement system. The filter to be tested is fitted between the untreated gas and purified gas measurement systems. A white oil (DAB 10) is atomized in the metering system such that the resulting particle spectrum at the untreated gas measurement point is comparable to that arising in practice on machine tools. The metering system is designed such as to ensure a residence time of the particles in the air (time between creation and filtration of the particles) comparable to that occurring in machine tools. The average residence time of the particles arising on machine tools was determined by simulation analyses performed by the University of Stuttgart's institute of building energetics (IGE). Further simulation analyses conducted at the Institute of Technical Thermodynamics and Refrigeration in Karlsruhe showed that under the designated conditions, a change in the degree of fractional filtration caused by the change in liquid-vapour equilibrium is of only minor significance, and that the white oil (DAB 10) is therefore suitable for test purposes. As soon as the burn-in tests are completed, the first filters can be tested.
metal working
Type of hazard:dangerous substances, design of work and technology, work organization/safety and health management
Catchwords:design of plants and procedures, fire and explosion protection, technical protective measures (exposure reduction/ protective devices)
Description, key words:metal working fluid emissions, collection, exhaust, filtration, fire and explosion protection